动力电池模组PACK激光焊接工艺解决方案
发布时间: 2021-07-07
动力电池的激光焊接部位多,其材料主要是铝合金,少量部位采用紫铜、镍等材料,还有极少数采用不锈钢作为电池外壳。在这些材料中,镍和不锈钢的激光焊接工艺相对较为简单,也更为成熟,但铝合金和紫铜的激光焊接依然存在较多难点。除材料特性的影响之外,焊接接头的状态也会对焊接效果产生较大影响。
一、待焊接的材料种类及状态
待焊材料种类:
当铝合金和紫铜作为焊接材料时,常规激光焊接效果不良的主要原因在于:
1. 两者对光纤激光的吸收率较低,导致焊接过程不稳定。
2. 导热性能较好,焊缝成型困难,易产生气孔。
虽然这两种材料有相似之处,但也存在差异:
- 铝合金对光纤激光的吸收率高于紫铜。
- 紫铜的导热性能优于铝合金。
铝合金解决方法:
1. 采用较小的聚焦光斑(0.1mm-0.3mm)。
2. 焊接速度控制在60mm/s以上。
3. 采用光纤-半导体激光复合焊接。
4. 采用摆动焊接。
紫铜解决方法:
1. 采用较小的聚焦光斑(0.02mm-0.2mm)。
2. 焊接速度建议在100mm/s以上。
3. 采用摆动焊接。
待焊材料状态:
材料的表面清洁度和预处理程度会显著影响焊缝质量。
1. 材料表面有杂质:
- 问题:焊缝存在气孔,密封性和强度不足。
- 解决方案:焊接前去除油污、水渍等杂质。
2. 铝合金表面氧化物未清理:
- 问题:焊缝气孔较多,密封性和强度不足。
- 解决方案:焊前去氧化膜处理,并尽快焊接。
3. 材料待焊处加工粗糙:
- 问题:成型不均匀,外观较差,易焊漏。
- 解决方案:进行机加工处理,确保表面平整无变形。
二、焊缝所属部件类型及要求
目前主流的汽车动力电池包括方形电池、圆柱电池和软包电池。方形电池最常用,激光焊接部位也最多,其他两类电池的市场份额和焊接需求相对较少。
常见焊接问题包括强度不足、密封性差和成型不良。这些问题通常由焊接工艺选择不当和焊接部位结构导致。
1. 软包电池部件-极耳/汇流排:
- 难点:材料薄,多片叠焊易虚焊,导致强度不足和导电性差。
- 解决方案:控制来料平整度;设计高性能夹具,控制装夹间隙。
2. 圆柱电池部件-21700电池盖帽:
- 难点:材料薄,易烧穿,强度不足。
- 解决方案:控制来料一致性;设计高性能夹具;选用小纤芯光纤激光器,采用振镜高速焊接(300mm/s以上)。
3. 动力电池模组:
- 难点:熔深要求大,焊缝成型差。
- 解决方案:选用50μm~100μm纤芯激光器,使用高功率进行高速焊接(80mm/s以上)。
4. 方形电池部件:
- 难点:气孔多,易出现爆点,密封性不足。
- 解决方案:提高待焊部位清洁度;选用50μm纤芯光纤激光器,适当提高焊接速度。
5. 壳体封口:
- 难点:气孔多,易出现爆点,密封性不足。
- 解决方案:提高待焊部位清洁度;选用50μm纤芯光纤激光器;采用小纤芯光纤激光器+半导体激光器复合焊接。
6. 汇流排:
- 难点:材料薄,多片叠焊易虚焊,强度不足。
- 解决方案:控制来料平整度;设计高性能夹具;选用小纤芯光纤激光器,采用摆动焊接。
7. 侧板:
- 难点:焊接部位多,效率要求高。
- 解决方案:选用高功率光纤激光器,进行远程扫描焊接。
8. 软连接:
- 难点:材料薄,多片叠焊易虚焊,强度不足。
- 解决方案:控制来料平整度;设计高性能夹具;选用小纤芯光纤激光器,采用摆动焊接。
该解决方案全面应对了动力电池模组激光焊接中的挑战,确保高质量和高效率的生产。
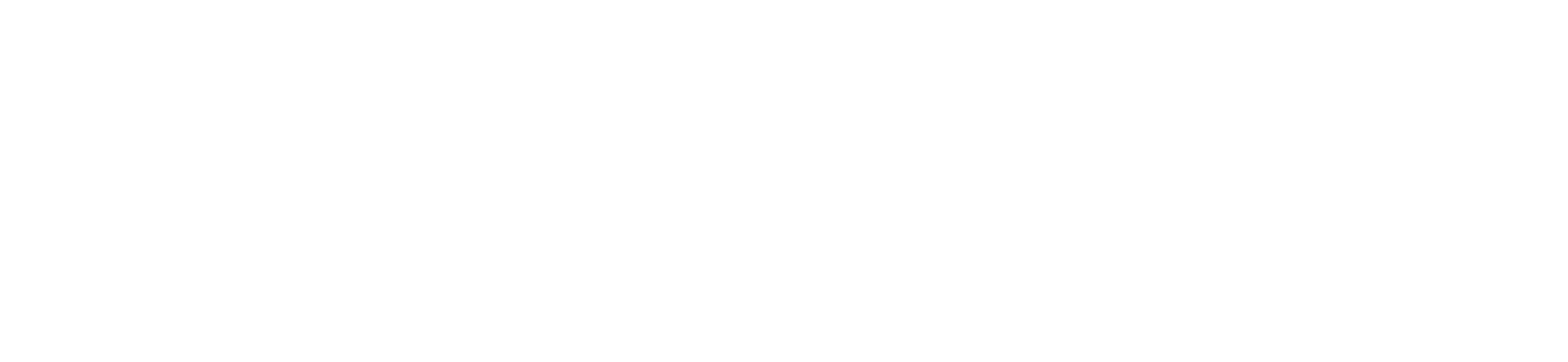
联系方式
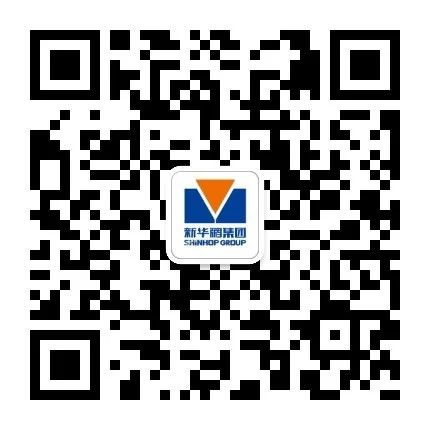
扫码关注公众号
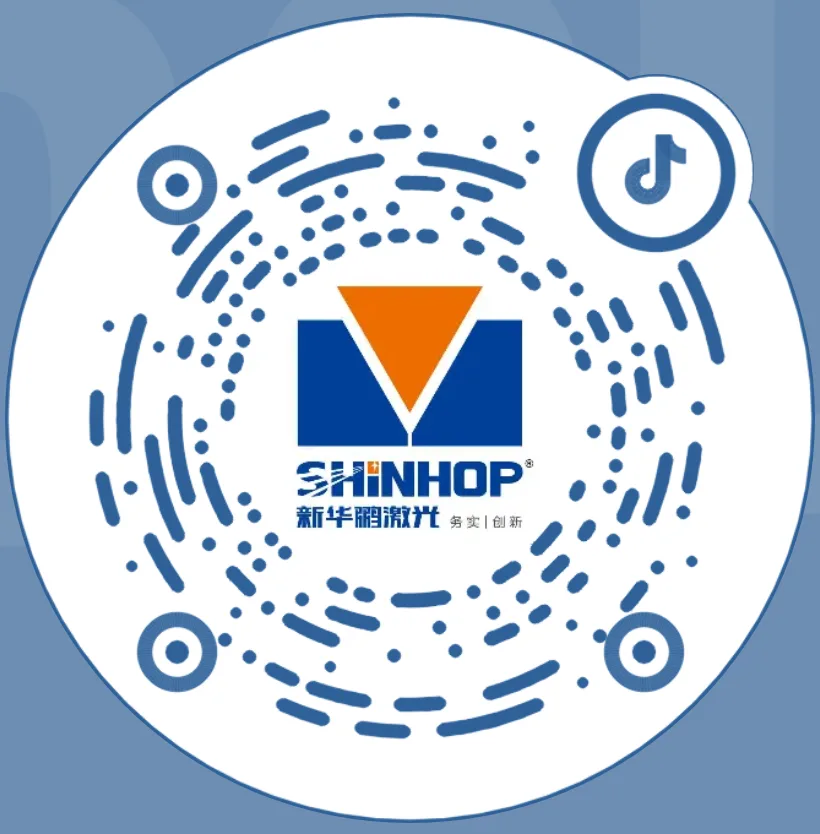
扫码关注抖音号